Was ist QFD?
QFD (Quality Function Deployment) wurde zu Beginn der siebziger Jahre in Japan von Prof. Yoji Akao (mit Shigeru Mizuno) entwickelt und hat über die USA in den 90er Jahren des vergangenen Jahrhunderts Eingang nach Europa gefunden. Der Name Quality Function Deployment wird allgemein als wenig aussagekräftige Übersetzung des japanischen „hin-shitsu ki-no ten-kai“ angesehen. Trotzdem hat er sich weltweit etabliert als Bezeichnung für eine Methode zur kundenorientierten Produktplanung. So definiert die ISO-Norm 16355-1:2015-12 QFD als „a method to assure customer or stakeholder satisfaction and value with new and existing products by designing in, from different levels and different perspectives, the requirements that are most important to the customer or stakeholder.“
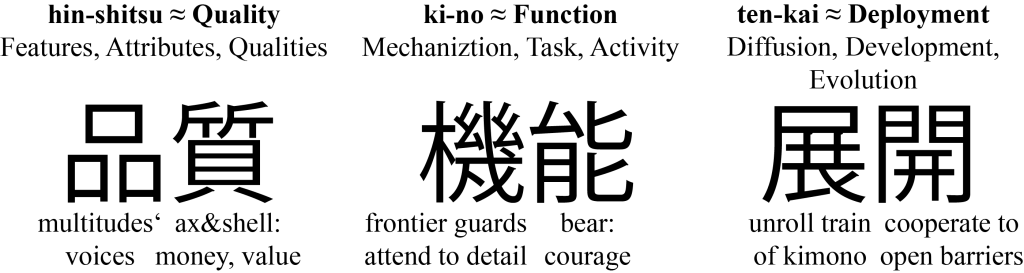
QFD ist damit keine Qualitätssicherungsmethode im herkömmlichen Sinne, sondern wird als ein vorbeugendes Werkzeug zur Produktdefinition eingesetzt. Es ist eine Qualitätsmethode zur Ermittlung der Kundenanforderungen und deren direkten Umsetzung in die notwendigen technischen Lösungen. Der strategische Ansatz ist die Trennung der Kundenanforderungen (WAS) von den technischen Lösungsmerkmalen (WIE), um zu verhindern, dass ohne genaue Kenntnisse der Kundenanforderungen sofort Produktmerkmale festgelegt werden. Es ist ein systematischer Weg, der sicherstellt, dass die Festlegung der Produktmerkmale durch die Entwicklung und die anschließende Auswahl der Produktionsmittel, Methoden und Kontrollmechanismen ausschließlich von den Anforderungen der zukünftigen Kunden bestimmt werden. QFD ist deshalb ein wichtiger Bestandteil der vorbeugenden Qualitätssicherung und erfüllt damit eine der Erfordernisse von ISO 9000ff bzw. QS9000. Seit Ende 2015 ist es zudem in der ISO-Norm 16355-1:2015-12 mit dem deutschen Titel „Anwendung von statistischen und verwandten Methoden für neue Technologie und für den Produktentwicklungsprozess – Teil 1: Allgemeine Grundsätze und Perspektive der QFD-Methode“ beschrieben.
QFD löst mehrere, miteinander verbundene Aufgaben
- Direktes Einbringen der Kundenanforderungen.
- Definieren der Wettbewerbsvorteile durch die für den Kunden überraschenden Lösungen (begeisterter Kunde).
- Verstehen der verschiedenen Anforderungen von Kunden, Entwickler, Produzenten, Verkäufer.
- Erstellen der Bewertungsprofile, Wechselbeziehungen der einzelnen Anforderungen/Lösungsmerkmale.
- Festlegen der für die Qualität des Produktes aus Kundensicht wichtigen und daher für den Verkaufserfolg entscheidenden Produktmerkmale.
- Ermitteln der Kosten – Wert Relationen.
- Einheitliche, methodische Kommunikation der Ziele für alle Bereiche, einschließlich einer nachvollziehbaren Dokumentation des gesamten Prozesses.
Ablauf von QFD-Projekten
Zuerst gilt es die Kundenanforderungen zu ermitteln. QFD legt dabei Wert auf einen direkten Kundenkontakt zur Erhebung der wahren Stimme des Kunden (“Voice of the Customer (VoC)”). Als “Kunde” wird dabei nicht nur der Käufer eines Produktes gesehen (“Externer Kunde (Käufer)”), sondern auch alle Beteiligten des Umsetzungsprozesses (“Interner Kunde”). Die meist sehr groben, vagen Äußerungen der Kunden müssen anschließend in definierte, aussagefähige und weitgehend messbare Kundenanforderungen (Kundenbedürfnisse) umgewandelt werden, ohne sie dabei zu verfälschen. Zur Unterstützung und Dokumentation wird dazu oft die 6-W Tabelle herangezogen (wer, was, wo, wann, wieviel, warum). Unterschieden wird oft auch gemäß der sog. Kano-Klassifiaktion in Basisanforderungen (oft nicht ausgeprochen, werden vorausgesetzt), Leistungsanforderungen (werden genannt, sind meist messbar) und Begeisternde Anforderungen (oft nicht genannt, nur als Bedürfnis angedeutet, werden als Überraschung gewertet, entscheiden oft über Verkaufserfolge).
Für jede ermittelte Anforderung an ein neues Produkt werden dann verschiedene Prioritäten durch den zukünftigen Kunden vergeben, die dann durch festgelegte Regeln in einem Qualitätsplan zusammengefasst und gewichtet werden.
Anschließend werden über eine erste Korrelationsmatrix (QFD-Matrix) alle möglichen, verschiedenen technischen Lösungsmöglichkeiten (z. B. Qualitätsmerkmale, Produktfunktionen) mit den Kundenanforderungen verknüpft und die Beziehung bewertet: keine, schwache, mittlere oder starke Beziehung. Durch die anschließende Auswertung (“das Lesen”) der Matrix werden die Lösungen ermittelt, die den höchsten Erfüllungsgrad zu allen Anforderungen haben. Aber es werden auch die Lösungen ermittelt, die keine (oder sehr schwache) Beziehungen zu den Anforderungen besitzen (und daher meist unnötig sind (“overengineering”)) oder die Anforderungen, die nicht erfüllt sind.
Im “Dach” der QFD-Matrix werden durch einen paarweisen Vergleich die Beziehungen der verschiedenen Lösungsmerkmale untereinander (positiv, negativ, neutral) festgelegt. Sie ermittelt vor allem Konflikte dieser Lösungsmerkmale untereinander, die dann im einzelnen , meist durch Kompromisse, gelöst werden müssen. Deshalb wird diese Matrix auch oft als Konfliktmatrix bezeichnet. In neuerer Zeit wird sehr erfolgreich auch die Methode TRIZ oder WOIS (widerspruchsorientierte Innovationsstrategie) eingesetzt, um umstrittene (“faule”) Kompromisse durch neue, innovative Lösungen zu ersetzten.
Das Ergebnis ist eine nach Kundenprioritäten ermittelte Produktplanung. Zur Auswertung und Dokumentation wird das “House of Quality (HoQ)” (siehe Abbildung) eingesetzt, das die QFD-Matrix und die verschiedenen Bewertungstabellen, -listen und weitere Dokumentationen zusammenfasst darstellt. Damit werden auch übersichtlich die verschiedenen Wechselwirkungen der vielen, oft komplexen Zusammenhänge verdeutlicht. Durch die Verbindung von Target Costing und QFD in einem Zielkostendiagramm kann zudem eine aus Käufersicht qualifizierte Zielkostenaufteilung vorgenommen (“Design to Cost”) werden.
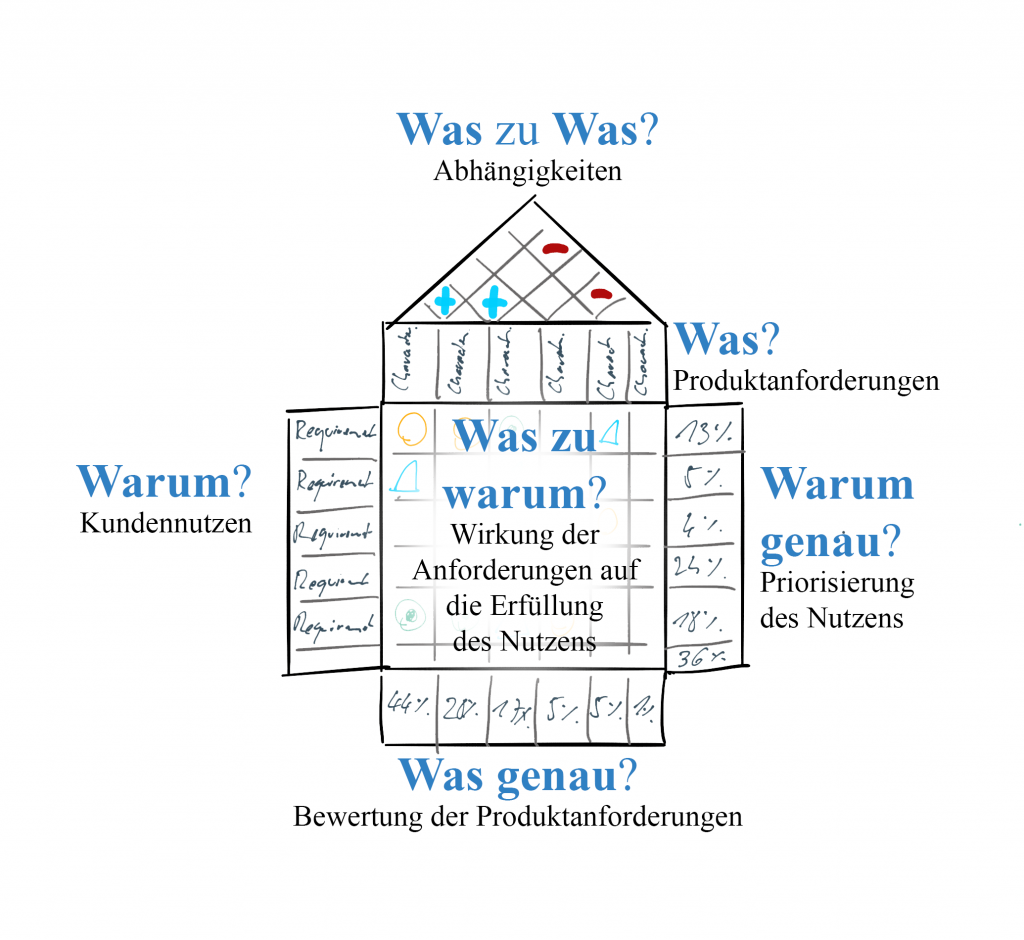
In drei (oder mehr, oft verzweigten) weiteren “Houses of Quality” wird die Umsetzung dieser Anforderungen in Produktgestaltung, Fertigung, Dienstleistungen und Prozesskontrolle festgehalten. Das Prinzip ist sehr einfach: alle ermittelten Lösungsmerkmale werden an das nächste “House of Quality”, das den nächsten Prozessschritt beschreibt, als eine Anforderung weitergegeben und wieder in einer Matrix mit den dort ermittelten Lösungen verknüpft. Dies ergibt eine Kette oder ein Netz von HoQ’s, dem sog. “deployment”, deren Struktur sich an die Prozessschritte oder Projektplänen anlehnt. Vorteilhaft ist dann die Weiterführung der Ergebnisse bei Konflikten oder wichtigen Merkmalen mit Hilfe von anderen Qualitätsmethoden wie der FMEA. Nachstehend ein Vorschlag für einen QFD-Deployment erarbeitet in Best Practice Workshops initiiert vom QFD-ID.

Voraussetzungen für den Einsatz von QFD
Die Anwendung von QFD erfordert eine stark teamorientierte Arbeitsweise im Unternehmen, die Unterstützung des Management ist eine notwendige Voraussetzung. Nicht nur die Mitarbeit der Entwicklungabteilungen ist zwingend erforderlich, sondern auch die von Marketing/Vertrieb. Der Zeitaufwand für eine QFD-Session darf dabei nicht unterschätzt werden. Die Arbeitsgruppen, werden meistens von einem neutralen QFD-Moderator, der für die Einhaltung der QFD Regeln verantwortlich ist, geleitet. Der Einsatz einer QFD spezifischen Applikationssoftware zur Unterstützung der Auswertung und Dokumentation ist empfehlenswert.
QFD ist ein sensibles Werkzeug. Eine aus Unkenntnis der verschiedenen Möglichkeiten des Einsatzes von QFD falsche Anwendung vergeudet nur Zeit. Dies gilt insbesondere bei einer unflexiblen Anwendung des House of Quality. Hier gilt der Satz von Akao: “Copy the spirit, not the form”.
Vorteile bei voller Anwendung des QFD Verfahrens
- Schneller Beginn der Entwicklung.
- Weniger Änderungen.
- Kürzere Produktionszeit.
- Profitables Produkt.
- Zufriedene, oft begeisterte Kunden.
Damit ist heute QFD eines der erfolgreichsten Werkzeuge zur Produktplanung und Produktdefinition und hat den Begriff “Qualität” nachdrücklich verändert: Es gibt keine “gute” oder “schlechte” Qualität mehr im herkömmlichen Sinne, sondern sie ist festgelegt durch die Erfüllung der Bedürfnisse des Käufers und deren Erfüllungsgrad im Qualitätsdreieck: Produktqualität, Kosten und Zeit.
Weitere Literatur finden sie hier!